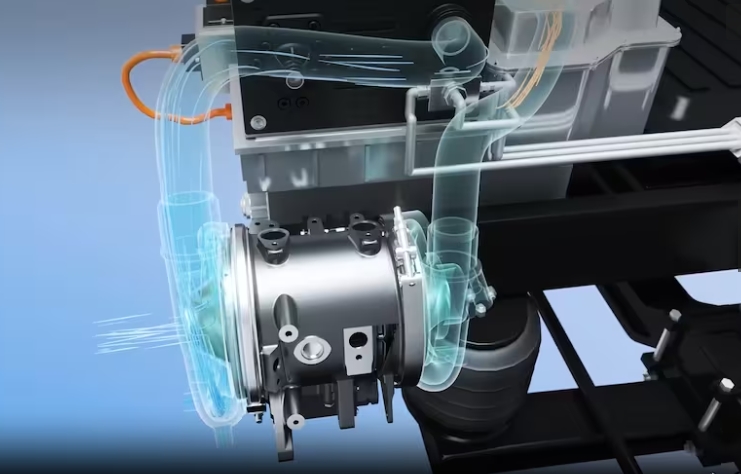
Exploring the Mechanics of a Fuel Cell Turbocharger: Are You Prepared?
Garrett Motion, renowned experts in turbocharging technology, formerly known as AiResearch, have successfully devised a method to harness the energy present in the hot water-vapor exhaust stream of a fuel cell.
In the race to secure a position in the rapidly evolving electric vehicle industry, established suppliers of mechanical parts in the automotive sector are swiftly making their mark. Garrett Motion, a renowned global provider of turbochargers, e-turbos, traction drives, and various cooling compressors, has strategically positioned itself as a key player in the realm of hydrogen fuel cell technology. With a specialized focus on manufacturing the essential compressor component responsible for supplying oxygen to fuel cells, Garrett Motion has secured its niche in this emerging market.
Similar to a turbocharged engine, when compressed air enters a fuel cell, it initiates a reaction that generates heat, resulting in the release of hot exhaust. Garrett Motion’s innovative third-generation compressor design harnesses this energy from the exhaust, similar to how a turbocharger operates. To gain further insights into the parallels and distinctions between turbocharging a fuel cell and a combustion engine, we conducted an interview with Craig Balis, Chief Technology Officer at Garrett. Let’s delve into the details.
Similar Form Factor
In both turbocharging applications, a common element is the presence of an impeller that allows the hot exhaust to expand, thereby transferring rotational energy to a compressor turbine connected to the same shaft. However, in the case of turbocharging a fuel cell, an additional component comes into play: an electric motor that is also connected to the shaft and primarily responsible for driving the system. This electric motor takes on the majority of the workload in this setup.
In comparison to a highly stressed turbocharged engine, the exhaust from a fuel cell operates at lower temperatures, reaching a maximum of approximately 400 degrees Fahrenheit. This temperature difference simplifies the selection of materials, as there is no need for high-nickel or exotic alloys. Instead, steel and aluminum alloys can be used, which are more readily available. While managing the water vapor produced by the fuel cell does present some challenges, such as erosion of specific materials and components, these challenges have been well understood and can be effectively addressed.
20 Percent Energy Savings, No Lag
Due to the lower temperature, there is less energy available to harness in a fuel cell’s compressor compared to a highly stressed gas turbocharger. However, the workload for the fuel cell’s compressor is significantly lower than that of a gas turbocharger in a high-performance engine. The primary function of the fuel cell is to generate electricity, and the compressor ranks as the second largest consumer of electricity in a fuel cell electric vehicle (FCEV), following the traction motor. The power consumption of the compressor typically ranges from 10-12kW for smaller compressors to 25-30kW for heavy-duty applications.
By incorporating an exhaust expander “turbo,” the electrical energy consumption of the compressor can be reduced by 20 percent, resulting in increased efficiency and extended range for fuel cell electric vehicles (FCEVs). In production FCEVs, the instant response of battery-electric “hybrid” systems eliminates any perceptible “turbo lag” for the driver, as these vehicles rely on stored energy for immediate acceleration. Furthermore, the electric compressor rapidly ramps up, causing exhaust pressure to rise and subsequently reducing the electrical load on the compressor.
Lower Speeds
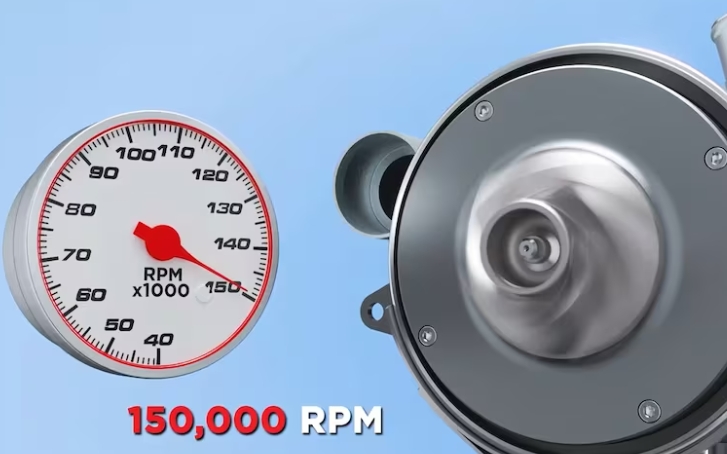
Garrett’s fuel-cell compressors achieve speeds of approximately 150,000 revolutions per minute (rpm), which, although lower than internal combustion engine (ICE) turbos, is still high for an electric compressor. This high-speed operation allows for a more compact package size. However, a challenge with the fuel-cell compressor is that its synchronous permanent-magnet electric motor must spin at the same speed, eliminating the need for a reduction geartrain. This speed is approximately 10 times faster than that of a traction motor, making it difficult for traditional sensors to measure turbine speed and position accurately. To overcome this, Garrett employs advanced software algorithms that infer turbine speed and position ten times per revolution based on voltage and current measurements.
Oil-Free Foil Bearings
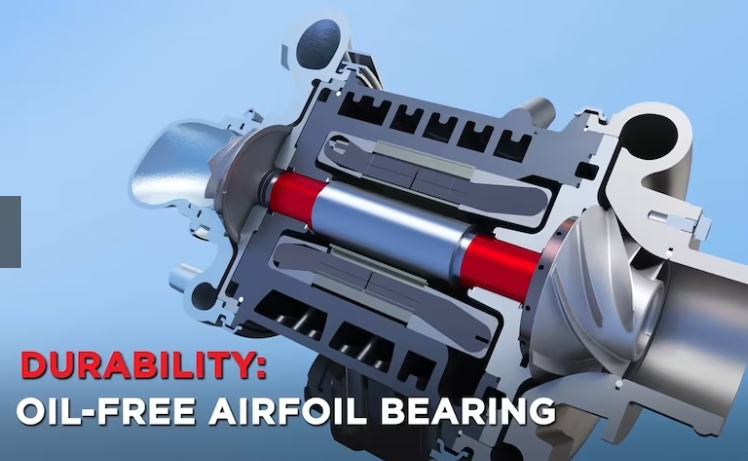
To prevent any oil contamination that could harm the fuel-cell membrane, the compressor shafts in fuel-cell systems utilize “air bearings.” These bearings incorporate an ultra-thin metallic foil that creates a cushion of air pressure between the shaft and housing. This air pressure is generated solely by the spinning shaft, allowing it to “lift off” from a stationary position and “land” when coming to a stop, without the need for external pressure. This design ensures that there is no contact between the shaft and housing, minimizing friction and the risk of oil contamination.
No Turbo Whistle
Aerodynamic noise, often associated with the distinctive whistle of traditional turbos, is minimized in fuel-cell compressors to ensure a quiet operation. The use of foil bearings not only helps reduce noise but also enhances the longevity of the compressor. These bearings are designed to withstand approximately 1 million start/stop cycles, providing durability and reliability to the system. As fuel cells operate silently, the focus is on maintaining a quiet and efficient compression process without unnecessary noise generation.
Featured in BMW iX5 Hydrogen and More?
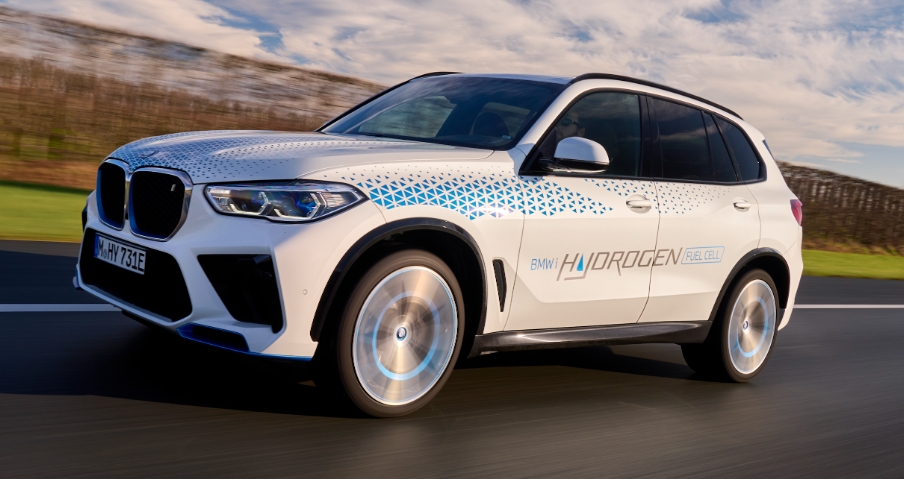
Garrett Motion’s fuel cell compressors have evolved over the years, starting with the first generation used in the limited production Honda Clarity FCEV. The second generation is currently in regular production for a few other fuel-cell vehicles on the market. Now, the third-generation compressor has been confirmed for production in the BMW iX5 Hydrogen. The BMW iX5 Hydrogen was first announced in 2020 and was recently unveiled in Antwerp in March 2023. With an impressive range of approximately 300 miles (WLTP cycle) and a quick refueling time of three to four minutes, the BMW iX5 Hydrogen is set to offer a compelling fuel cell electric vehicle (FCEV) experience. BMW is currently operating pilot fleets in selected markets to gather customer feedback and further refine their fuel cell technology. Garrett Motion’s collaboration extends beyond BMW, as the company has established partnerships with numerous global original equipment manufacturers (OEMs). This means that BMW is not the first and certainly won’t be the last automaker to bring a production vehicle equipped with a Garrett Motion fuel cell turbocharger to the market.